PCD wire drawing dies compare with TC
PCD (Polycrystalline Diamond) wire dies and TC (Tungsten Carbide) wire dies are both used in wire drawing processes, but they have some key differences in terms of their material properties, performance, and applications.


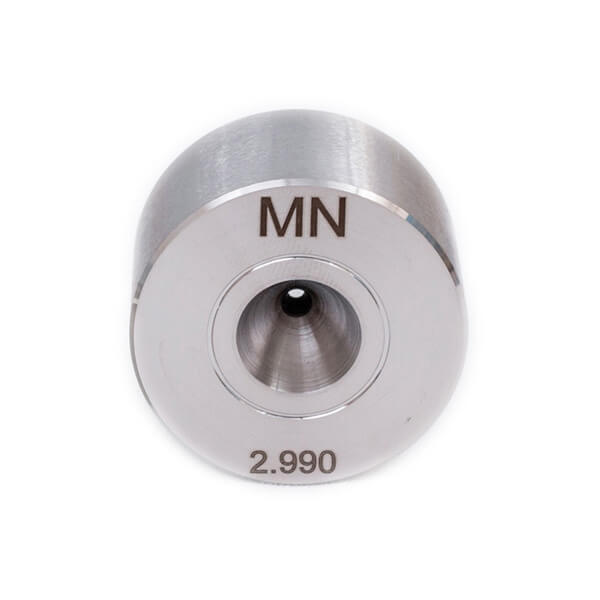



Material Properties:
- PCD wire dies are made from a synthetic diamond material that is extremely hard, wear-resistant, and has low friction. PCD is known for its excellent thermal conductivity, which allows for efficient heat dissipation during wire drawing process.
- TC wire dies, on the other hand, are made from tungsten carbide, which is a hard and dense material. Tungsten carbide is known for its high melting point and resistance to wear, but it has lower thermal conductivity compared to PCD.
Performance:
- PCD wire dies are known for their superior performance in terms of wear resistance, which results in longer die life and less frequent die changes. PCD wire dies also typically require less lubrication during the wire drawing process due to their low friction properties.
- TC wire dies are also wear-resistant, but they may have a shorter die life compared to PCD wire dies, especially when drawing harder or abrasive materials. TC wire dies may also require more frequent lubrication to prevent galling and reduce wear.
Applications:
- PCD wire dies are commonly used in wire drawing processes for non-ferrous metals, such as aluminum, copper, and their alloys. They are also suitable for drawing softer materials like plastics and fibers.
- TC wire dies are often used for drawing harder materials, such as steel, stainless steel, and other ferrous metals.