Kit PCD extrusion dies mandrel and matrix

Cable extrusion dies play a pivotal role in cable manufacturing.
Serving as essential tools for shaping cable materials into desired forms.
Understanding the key components of these dies is crucial for achieving efficient and precise cable production.
Here’s a breakdown of the main parts that constitute a cable extrusion die:
- Die Head: The die head is a critical component determining the geometry and size of the cable shape. Typically made from materials like alloy steel or hard alloy, it features the extrusion hole for the cable and auxiliary structures such as the feed port, heater, thermometer, etc.
- Screw: As the core component of the cable extruder, the screw acts as the power source pushing cable material from the hopper to the extrusion die. Constructed from materials like nickel-chrome-molybdenum alloy, screws ensure high strength and wear resistance, and their structure and size must be matched to the extrusion die for even material extrusion.
- Extrusion Head: Another crucial part determining the shape and size of the cable material. Typically made of robust materials such as hard alloy, the extrusion head incorporates a diverting device, filter screen, and adjusting device to ensure uniform material extrusion.
- Heater: This component softens the cable material, facilitating easy extrusion. Heaters, often electric or gas-based, vary in number and distribution based on the size and shape of the extrusion die.
- Control System: At the core of the extrusion die, the control system regulates parameters such as extrusion speed, temperature, and pressure. Comprising a temperature controller, pressure sensor, speed controller, etc., the control system can be customized to meet specific production needs.
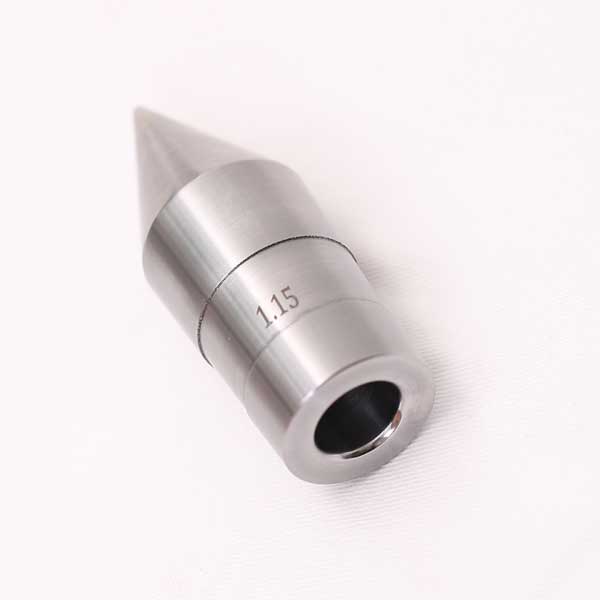
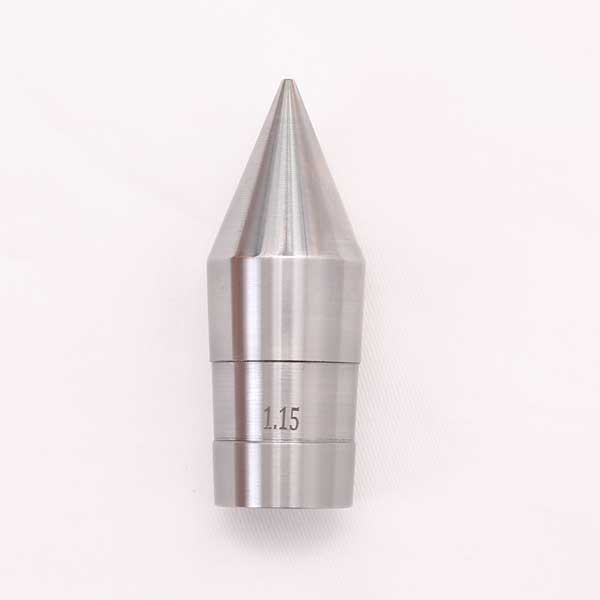
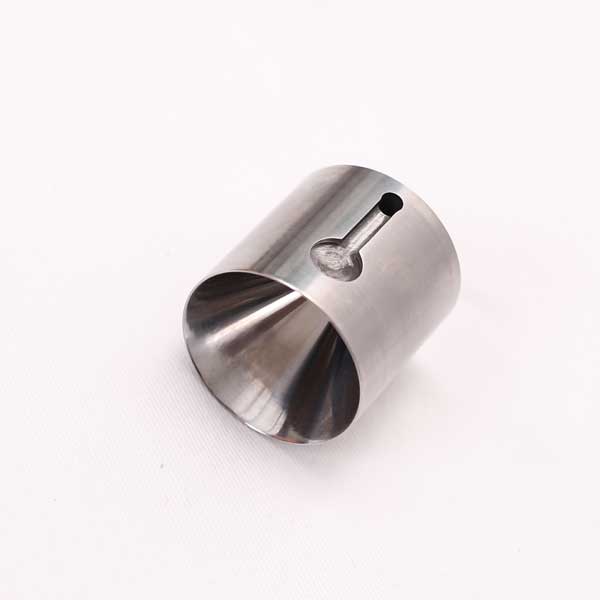
By comprehending the functions of these components and tailoring their design and usage, manufacturers can ensure the optimal performance and longevity of cable extrusion dies, ultimately enhancing the efficiency of cable production.